Publications
* denotes equal contribution.
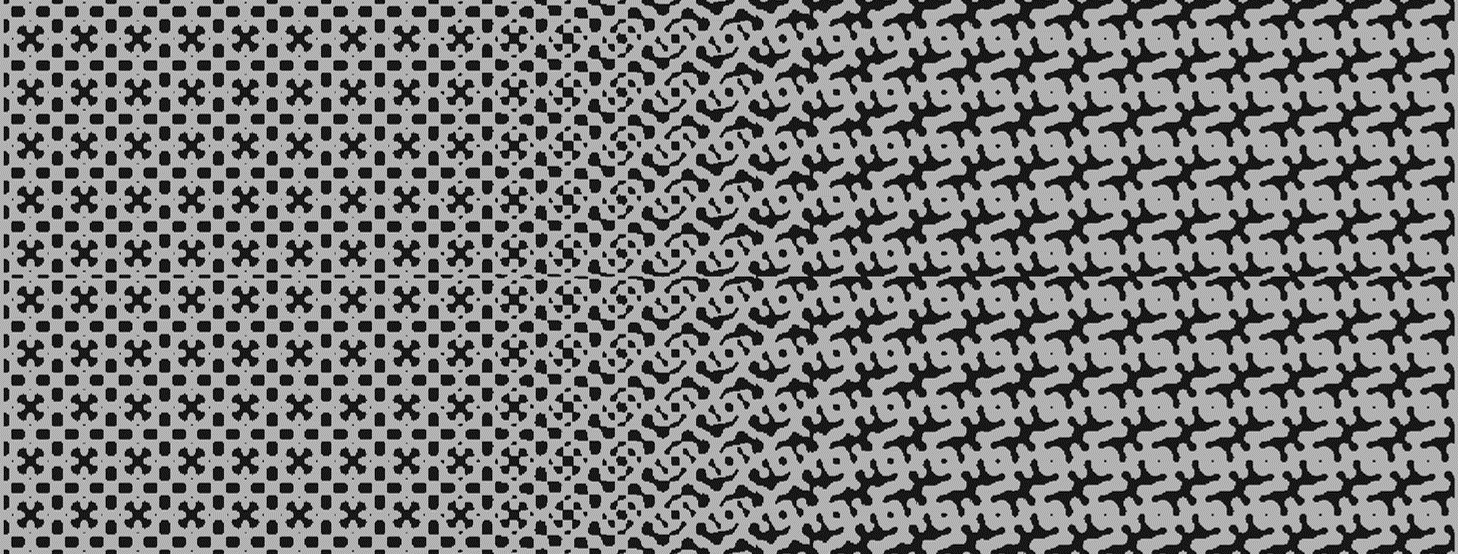
2024
2024
- MatDesPlanar structured materials with extreme elastic anisotropyJagannadh Boddapati , and Chiara DaraioMaterials & Design, 2024
Designing anisotropic structured materials by reducing symmetry results in unique behaviors, such as shearing under uniaxial compression. While rank-deficient materials such as hierarchical laminates have been shown to exhibit extreme elastic anisotropy, there is limited knowledge about the fully anisotropic elasticity tensors achievable with single-scale fabrication techniques. No established upper and lower bounds on anisotropic moduli exist. In this paper, we estimate the range of anisotropic stiffness tensors achieved by single-scale two-dimensional structured materials. We first develop a database of periodic anisotropic single-scale unit cell geometries using linear combinations of periodic cosine functions. The database covers a wide range of anisotropic elasticity tensors, which are then compared with the elasticity tensors of hierarchical laminates. We identify the regions in the property space where hierarchical design is necessary to achieve extremal properties. We demonstrate a method to construct various 2D functionally graded structures using this cosine function representation. These graded structures seamlessly interpolate between unit cells with distinct patterns, allowing for independent control of several functional gradients. When designed with unit cells positioned at extreme parts of the property space, these graded structures exhibit unique mechanical behaviors such as selective strain energy localization, compressive strains under tension, and localized rotations.
@article{boddapati2024planar, title = {Planar structured materials with extreme elastic anisotropy}, author = {Boddapati, Jagannadh and Daraio, Chiara}, journal = {Materials \& Design}, volume = {246}, pages = {113348}, year = {2024}, doi = {https://doi.org/10.1016/j.matdes.2024.113348}, publisher = {Elsevier}, }
2023
2023
- JMPSSingle-test evaluation of directional elastic properties of anisotropic structured materialsJagannadh Boddapati* , Moritz Flaschel* , Siddhant Kumar , Laura De Lorenzis , and Chiara DaraioJournal of the Mechanics and Physics of Solids, 2023
When the elastic properties of structured materials become direction-dependent, the number of their descriptors increases. For example, in two-dimensions, the anisotropic behavior of materials is described by up to 6 independent elastic stiffness parameters, as opposed to only 2 needed for isotropic materials. Such high number of parameters expands the design space of structured materials and leads to unusual phenomena, such as materials that can shear under uniaxial compression. However, an increased number of properties descriptors and the coupling between shear and normal deformations render the experimental evaluation of material properties more challenging. In this paper, we propose a methodology based on the virtual fields method to identify six separate stiffness tensor parameters of two-dimensional anisotropic structured materials using just one tension test, thus eliminating the need for multiple experiments, as it is typical in traditional methods. The approach requires no stress data and uses full-field displacement data and global force data. We show the accuracy of our method using synthetic data generated from finite element simulations as well as experimental data from additively manufactured specimens.
@article{boddapati2023single, title = {Single-test evaluation of directional elastic properties of anisotropic structured materials}, author = {Boddapati*, Jagannadh and Flaschel*, Moritz and Kumar, Siddhant and De Lorenzis, Laura and Daraio, Chiara}, journal = {Journal of the Mechanics and Physics of Solids}, volume = {181}, pages = {105471}, year = {2023}, doi = {https://doi.org/10.1016/j.jmps.2023.105471}, publisher = {Elsevier}, }
2022
2022
- PNASMechanical cloak via data-driven aperiodic metamaterial designLiwei Wang , Jagannadh Boddapati , Ke Liu , Ping Zhu , Chiara Daraio , and Wei ChenProceedings of the National Academy of Sciences, 2022
Mechanical cloaks are materials engineered to manipulate the elastic response around objects to make them indistinguishable from their homogeneous surroundings. Typically, methods based on material-parameter transformations are used to design optical, thermal, and electric cloaks. However, they are not applicable in designing mechanical cloaks, since continuum-mechanics equations are not form invariant under general coordinate transformations. As a result, existing design methods for mechanical have so far been limited to a narrow selection of voids with simple shapes. To address this challenge, we present a systematic, data-driven design approach to create mechanical cloaks composed of aperiodic metamaterials using a large precomputed unit cell database. Our method is flexible to allow the design of cloaks with various boundary conditions, multiple loadings, different shapes and numbers of voids, and different homogeneous surroundings. It enables a concurrent optimization of both topology and properties distribution of the cloak. Compared to conventional fixed-shape solutions, this results in an overall better cloaking performance and offers unparalleled versatility. Experimental measurements on additively manufactured structures further confirm the validity of the proposed approach. Our research illustrates the benefits of data-driven approaches in quickly responding to new design scenarios and resolving the computational challenge associated with multiscale designs of functional structures. It could be generalized to accommodate other applications that require heterogeneous property distribution, such as soft robots and implants design.
@article{wang2022mechanical, title = {Mechanical cloak via data-driven aperiodic metamaterial design}, author = {Wang, Liwei and Boddapati, Jagannadh and Liu, Ke and Zhu, Ping and Daraio, Chiara and Chen, Wei}, journal = {Proceedings of the National Academy of Sciences}, volume = {119}, number = {13}, pages = {e2122185119}, year = {2022}, doi = {https://doi.org/10.1073/pnas.2122185119}, publisher = {National Acad Sciences}, }
2020
2020
- MechMatAn analytical model for shape morphing through combined bending and twisting in piezo compositesJagannadh Boddapati , Shaswat Mohanty , and Ratna Kumar AnnabattulaMechanics of Materials, 2020
Bilayer piezo macro fibser composites (MFCs) with specific fiber orientations are experimentally known to undergo bending as well as twisting, under the action of an externally applied electric field. An analytical model is developed for this shape-morphing phenomenon using continuum mechanics and energy minimization considering material anisotropy. A detailed parametric study is carried out using a coupled electro-mechanical finite element model and the results are used to validate the analytical model. The analytical model quantitatively predicts the variation of curvatures with the system parameters (bilayer geometry and electric field magnitude) with good accuracy. The tendency of a bilayer to undergo pure bending, pure twisting or a helical deformation is predicted using stress-free strain mismatch between anisotropic layers. Both bending and twisting deformations are found to be strongly dependent on the fiber orientation, vary linearly with the applied electric field magnitude, independent of length and decrease with an increase in width or thickness of MFC.
@article{boddapati2020analytical, title = {An analytical model for shape morphing through combined bending and twisting in piezo composites}, author = {Boddapati, Jagannadh and Mohanty, Shaswat and Annabattula, Ratna Kumar}, journal = {Mechanics of Materials}, volume = {144}, pages = {103350}, year = {2020}, doi = {https://doi.org/10.1016/j.mechmat.2020.103350}, publisher = {Elsevier}, }